Spherical CoCrNi Powder
Formula | CoCrNi |
Synonyms | spherical CoCrNi particles, spherical CoCrNi powders, CoCrNi Powder, CoCrNi thermal spray powder, CoCrNi gas atomized powder |
Appearance | Black Powder |
Particle Size | 15-53 um, 45-105 um, can be customized upon request |
Melting Point | 1427 °C |
Density | Â 8.05 g/cm 3 |
Purity | 99% min |
Tensile Strength, Yield | N/A |
Description of Spherical CoCrNi Powder
Spherical CoCrNi powder is a high-performance alloy composed of cobalt, chromium, and nickel, known for its excellent mechanical strength, corrosion resistance, and high-temperature stability. The powder is typically produced through gas atomization, resulting in spherical particles that enhance flowability and packing density, making it ideal for additive manufacturing and powder metallurgy.
CoCrNi powder is used in aerospace for high-temperature components like turbine blades due to its excellent strength and corrosion resistance. It is also utilized in medical implants for its biocompatibility and durability, making it ideal for additive manufacturing of complex, high-performance parts.
Princeton Powder is a leading supplier of Spherical CoCrNi powder. We specialize in a comprehensive range of spherical powder products and possess extensive expertise in additive manufacturing (3D printing) industry. Spherical CoCrNi powder is for sale at a competitive price.
Chemical Composition
Chemical Composition (wt%) | ||||||||||
Item | Fe | Co | Mn | Si | Ni | Cr | Mo | W | Be | Cd |
CoCrNi | – | Bal. | – | – | 20-40 | 25-35 | – | – | ≤0.02 | ≤0.02 |
Oxygen≤500 ppm; Nitrogen≤100 ppm
Particle Size distribution
0-15μm, 15-53μm, 45-105μm, 45-150μm. (Various particle sizes can be customized)
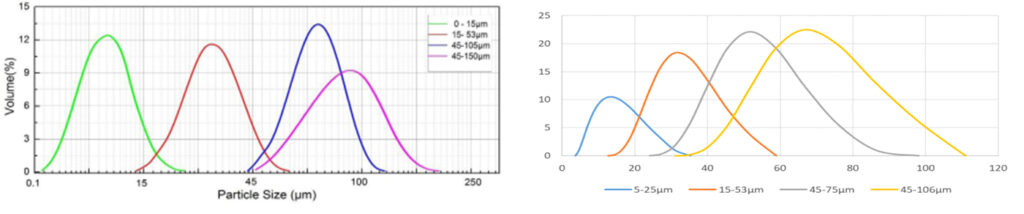
Applications
- Aerospace: Used in turbine blades, engine components, and other high-temperature applications.
- Medical Implants: Suitable for biomedical applications due to its biocompatibility.
- Additive Manufacturing: Ideal for 3D printing complex, high-strength parts.
Spherical CoCrNi Powder Powder Reference
- Equimolar CoCrNi medium entropy alloy (MEA) has a broad potential for industrial applications due to its excellent strength-ductility synergy. In this study, the emerging solid-state cold spray additive manufacturing (CSAM) approach was applied to fabricate bulk CoCrNi MEA deposits for the first time. However, due to its nature, CSAM normally results in limited metallurgical bonding and weak interfacial bonding between deformed particles, particularly for high-strength alloys such as the CoCrNi MEA used in this work.
CoCrNi alloy, composed of cobalt, chromium, and nickel, is known for its excellent mechanical strength and corrosion resistance, ideal for aerospace and medical applications. In contrast, CoCrW alloy, with tungsten instead of nickel, offers superior wear resistance and hardness, making it suitable for cutting tools and high-temperature components. The key difference lies in the enhanced wear resistance of CoCrW due to the presence of tungsten.